Fetching mountains...
1
3
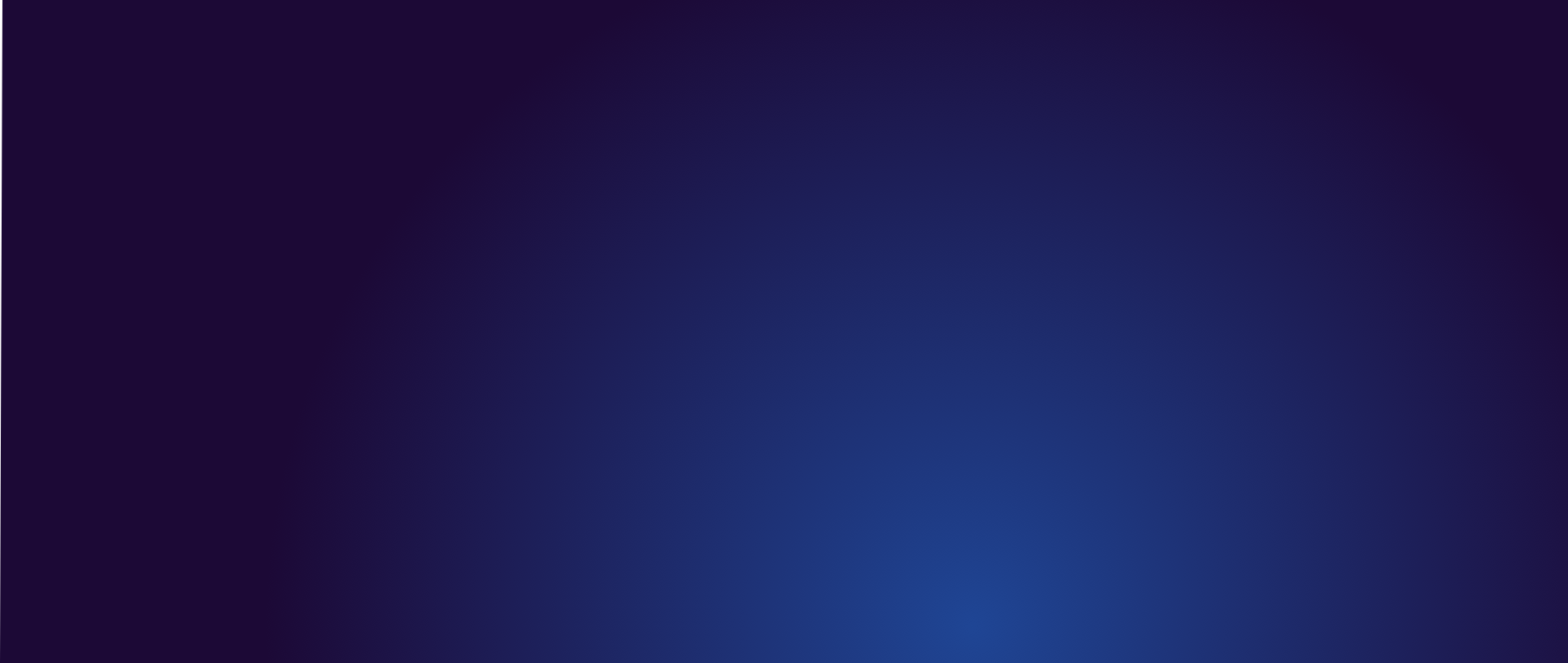
Our Company
Wizards is a family of studios, we specialize in building roleplaying games, trading card games, and digital games for all types of players.
Craft Our Next Game -
Join Us
Wizards is a family of studios, we specialize in building roleplaying games, trading card games, and digital games for all types of players.
Craft Our Next Game -
Join Us